Introduction
Adelaide Structural Engineers (ASE) was contracted by CH4 GLOBAL to conduct a comprehensive engineering inspection of their facility located at 11308 Lincoln Highway, Arno Bay, SA. This facility, previously operated by “CLEANSEAS,” was once used for tuna fish farming and has recently been repurposed for seaweed farming.
Building Description
The facility is divided into two areas: the Biofilter Area and the Tank Area. It is a single-story portal-framed building supported by a system of structural columns, roof trusses, rafters, and purlins. The roof is clad with metal sheeting, and the walls and ceilings are constructed using Bondor insulated panels to regulate internal temperature. The flooring primarily consists of concrete slab.
The building is located near the coast, exposing it to humid air with salt content. Additionally, seawater is extensively used for processing and seaweed farming, leading to increased humidity within the facility. The entire structure, including the cladding material, is constructed using steel. The prolonged exposure to a chloride- rich environment has resulted in varying degrees of corrosion on both structural and non-structural elements.
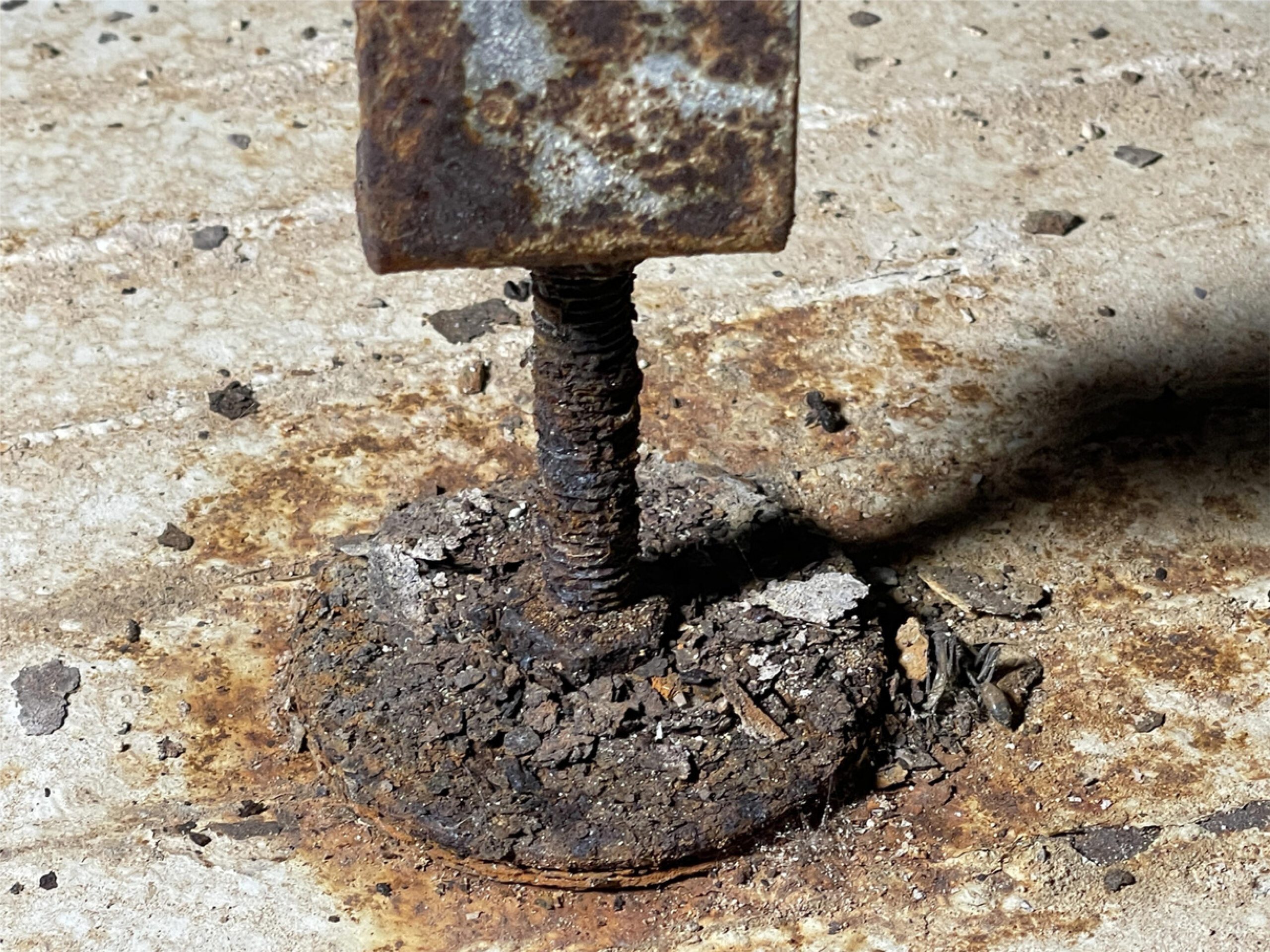
Project Description
The existing seaweed farming building along the coast in Port Lincoln, exhibited significant corrosion to the structural elements of the building raising concerns regarding the structural integrity of the building especially when some alterations were proposed to the building.
Challenge
The compromise to the structural integrity of the building provided a safety risk to the continued use of the building for the seaweed production. A thorough investigation of the issue was required, providing clear understanding of the structural integrity issue and a course of action to address the issue.
Solution
Adelaide Structural Engineers conducted a detailed inspection of the facility for the structural audit to identify the damage to the building, extent of the damage and provide remedial measures. The structural audit was completed utilising a risk based approach by considering the likelihood and consequence and impact of the structural failure. This provided a clear roadmap to the client to adequately plan for the repairs considering the plant operation and maintenance strategies without causing much disruption to the production.
Conclusion
The project successfully addressed the challenges of lift void closure, steel lintel installation for brick wall openings, and electrical conduit placement within the concrete slabs.
The structural engineering team played a crucial role in ensuring the safety, stability, and compliance of the renovations.
Through careful planning, thorough inspections, and precise designs, the building owner was able to repurpose the space while maintaining the structural integrity of the building, and the project was completed on time and within budget.
Our Clients
Our clients receive innovative and cost-effective solutions, working together from concept development, through to construction & commissioning and asset management – throughout the asset life cycle. Unlike typical consultants, we understand real project needs and push the boundaries to realise the project’s true potential.